A shockproof metal printed in 3D
Three-dimensional printing (3DP) is in full development, and it includes the printing of metal. A laser can fuse steel powder, and the resulting fluid can be deposited as with conventional processes. For example, Dirk Mohr, a researcher at ETH Zurich, has designed an optimised metal lattice to absorb shocks. The part-solid, part-hollow structure is arranged repeatedly to distribute the force of the impacts and reduce deformations. Mohr had explored this subject while studying for his degree, more than fifteen years ago. But such three-dimensional structures only existed on paper at the time: “It was only a pure game of the mind, impossible to achieve in practice. Given my engineering mentality, I had abandoned this work. But with the rise of additive manufacturing technologies, I was able to pull it back out of my drawer”. The new material is reminiscent of metal foams, a mass of steel that contains a large amount of air in small chambers. But the structure of the foams is more or less random, because the bubbles are formed at random by injecting gas into the molten metal. On the contrary, 3DP makes it possible to determine the structure of the material in its smallest details and to control its properties. Mohr and his doctoral student Colin Bonatti have developed an isotropic material. It resists pressure and impacts in all directions equally. The pores of the metal follow a shell design: a curved and complex structure, developed on a computer, optimised to distribute impacts and limit deformations. According to Mohr, this approach could be used to design custom-made elements, such as ultra-light mechanical energy absorbers or biomedical implants. “Industrial production, for example in the automotive industry, will have to wait for a reduction in the costs of metal additive manufacturing”. Lionel Pousaz CC BY-NC-ND
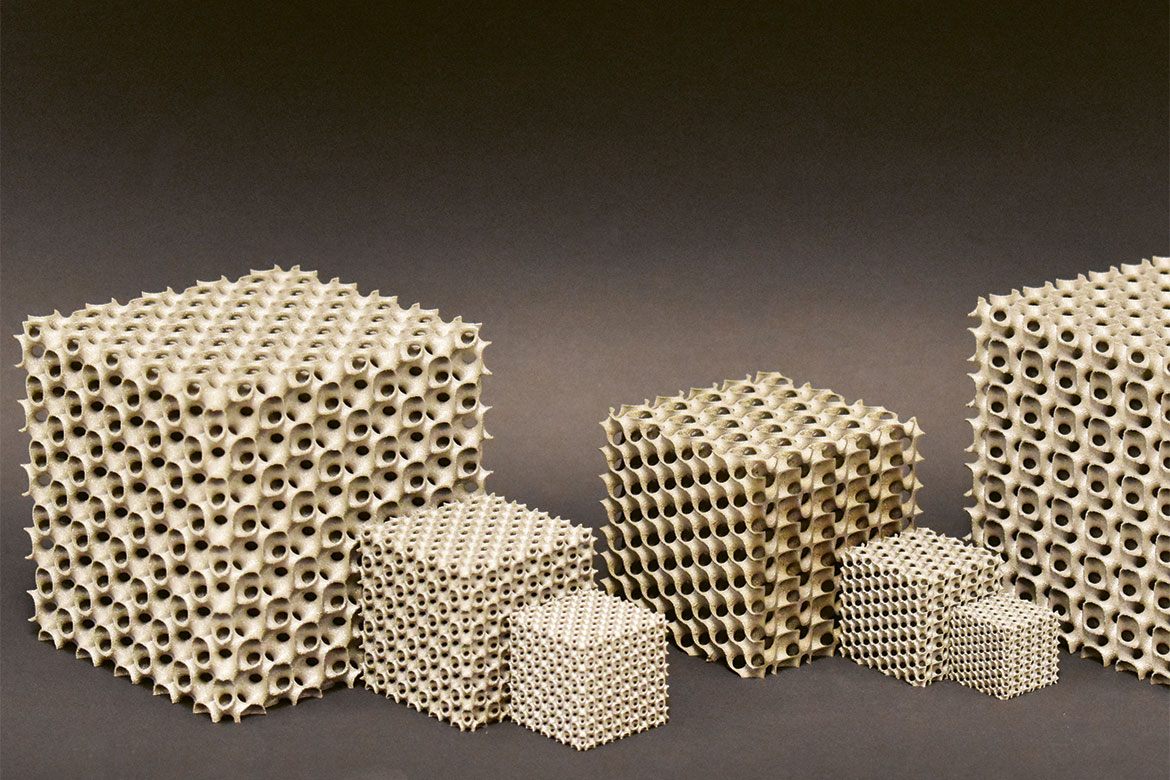
These metal blocks acquire special characteristics thanks to their repeating patterns of hollow spaces. | Image: Colin Bonatti, Dirk Mohr
Three-dimensional printing (3DP) is in full development, and it includes the printing of metal. A laser can fuse steel powder, and the resulting fluid can be deposited as with conventional processes. For example, Dirk Mohr, a researcher at ETH Zurich, has designed an optimised metal lattice to absorb shocks. The part-solid, part-hollow structure is arranged repeatedly to distribute the force of the impacts and reduce deformations.
Mohr had explored this subject while studying for his degree, more than fifteen years ago. But such three-dimensional structures only existed on paper at the time: “It was only a pure game of the mind, impossible to achieve in practice. Given my engineering mentality, I had abandoned this work. But with the rise of additive manufacturing technologies, I was able to pull it back out of my drawer”.
The new material is reminiscent of metal foams, a mass of steel that contains a large amount of air in small chambers. But the structure of the foams is more or less random, because the bubbles are formed at random by injecting gas into the molten metal. On the contrary, 3DP makes it possible to determine the structure of the material in its smallest details and to control its properties.
Mohr and his doctoral student Colin Bonatti have developed an isotropic material. It resists pressure and impacts in all directions equally. The pores of the metal follow a shell design: a curved and complex structure, developed on a computer, optimised to distribute impacts and limit deformations. According to Mohr, this approach could be used to design custom-made elements, such as ultra-light mechanical energy absorbers or biomedical implants. “Industrial production, for example in the automotive industry, will have to wait for a reduction in the costs of metal additive manufacturing”.
Lionel Pousaz